2016 News
Prepare for Winter: Keep Your Business Humming
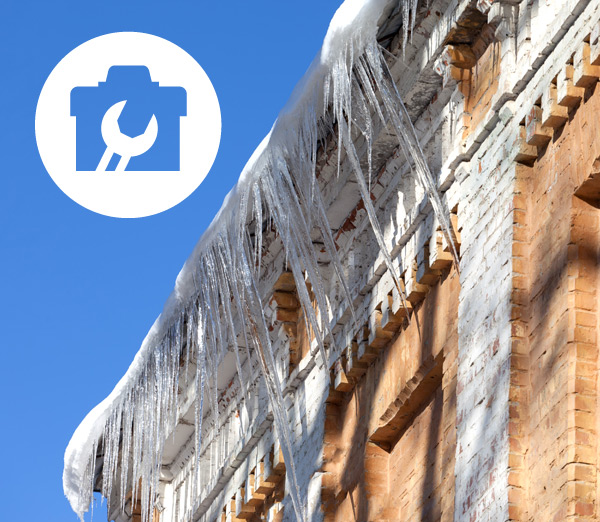
A little preventive maintenance in September and October can significantly reduce the risk of winter-related mechanical problems later on. Dale Drent, P.E., who directs Baker Group’s service business unit, offers some low-tech, DIY suggestions:
- Give your heating system a trial run. Force your system into heat mode for a few hours to make sure it runs properly. Some odor may occur due to dust that’s settled on the heat exchanger, but an odor that continues for more than 15 minutes should be checked by a professional. “Your heat exchanger is the hottest point in the whole building so it poses the greatest safety risk. Making sure it is controlled properly is critical,” says Drent.
- For natural gas systems, visually check the combustion air and the flue gas to make sure there are no obstructions. “When the system is idle all summer, sometimes things get into the piping, such as birds that make nests,” Drent says.
- If outdoor temperature sensors regulate your building’s heat, check their calibration. If they are not properly calibrated, your heating unit can malfunction.
- Check to be sure furnace filters are clean. Dirty air filters impair airflow, make it difficult to heat the space and shorten the life of the heat exchanger.
- Inspect for cracks in the building’s exterior. Cold air seeping in through walls, windows, doors and other cracks can cause pipes to freeze and burst. “When you are trying to maintain a 70-degree difference between the inside and outside, insulation is extremely important – for comfort as well as avoiding significant repair costs,” Drent says. If you are concerned about the status of the insulation in your building, a thermal imaging scan will pinpoint areas that have been compromised.
- If your building has sprinkler piping in the ceiling cavity of cooler vestibules or entryways, those may be at high risk of freezing or breaking. To know for certain, please contact Baker Group.
In your home, Drent also recommends making sure the battery in your thermostat has plenty of life in it: “If your battery goes dead and the heating system doesn’t get the signal to come on, it can result in frozen pipes.” Also keep furniture three to four inches away from diffusers and air return vents in floors, walls and ceilings to ensure adequate heat, efficiency and overall safety.
For commercial clients, Baker Group also offers a Preventive/Predictive Maintenance Program to extend equipment life, reduce energy cost and minimize downtown risk.
About Baker Group
Founded in 1963 and with more than 500 employees across Iowa, Baker Group is the Midwest’s premier full-service specialty contractor providing mechanical, sheet metal, electrical, building automation, process automation, security systems, fire alarm systems, parking/revenue controls and 24/7/365 service.
News
Best of Des Moines 2024
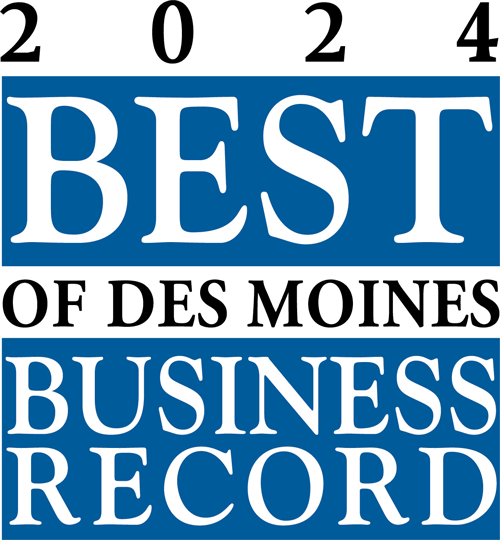
Baker Group was recognized by readers of the Des Moines Business Record for Des Moines' Best Mechanical Contractor for the 18th consecutive year.